|
|
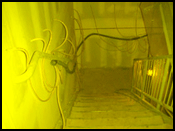 |
A recent series of tests has shown that by imploding controlled amounts of warm air in wall and ceiling cavities you can reduce wall damage and the problems associated with molds.
We used a machine specifically designed and manufactured for wall drying to rid walls of their wetness, even with fiberglass insulation, and walls having latex paint and vinyl wall paper on them.
|
This machine that we tested over several months is the Injectidry® Trapped Moisture Ventilating System, which is manufactured in the State of Washington by Injectidry Systems, Inc. What was shown through repeat tests is that the drying system displaces moisture by forcing in warm dry air through 7/32 inch holes that are drilled above the sill (bottom) plate, but behind the baseboard. Within a matter of hours, porous building materials started to give up their saturation and within one or two days completely dried the wall cavities and wall materials to pre-existing condition. Walls having wet fiberglass insulation took a day or two longer to dry. |
|
|
CONCLUSION:
Assuming the flooding condition was caused from fresh water, there is no history of prior flooding, and the drying system was in place within the first 12 hours, there were no visual signs of unwanted molds forming in or behind wall materials after drying. Yet, when the Injectidry® was not used, visible molds did develop inside wall cavities within a week, even when traditional building |
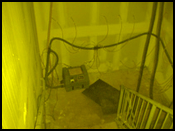
|
drying methods were used, such as with forced air movement and building air exchanges of dryer outside air. When the Injectidry® System was used behind non-porous wall paneling, vinyl wall paper, floor to ceiling glass mirrors and marble covered walls, the interior walls, dried within a matter of two to three days, when walls did not have an insulation in them. Plaster and gypsum-based wall materials were carefully monitored, they appeared to maintain their structural integrity, and there was no indication that any of the wall coverings required repair or touch-up, except surface vacuuming of dust. What was surprising, is how well the Injectidry® worked with built-in wall cabinets. None of the expensive back-wall paneling materials so far have warped, delaminated, or discolored from flooding. Especially when the Injectidry® System was installed within two days and allowed to dry out wet walls for an average of three days. "I can only imagine that both the homeowners and insurance adjusters were happy with the drying results and material damage cost savings."
by Patrick Moffett, Industrial Hygienist, Environmental Management & Engineering, Inc.
Respiratory Arrest!
Could this be you?
"My son is in intensive care and has stopped breathing" were the first words heard by the project manager on a water damage job. What a great way to start a day! Details to follow... Too often we fail to realize the absolute necessity of ensuring the complete dryness of structures on which we work. Many times contractors fail to measure the moisture content of the interior walls, ceilings, etc. or do not complete the drying process. The drying process is finished only when the structure reaches equilibrium with normal environmental conditions present. This is a point at which no further loss or damage will occur and assessments and/or repairs can be made. When drying is not done, problems can occur such as a contractor experienced recently. The contractor received a call from a previous customer reporting a new water damage. The scenario was fairly typical and sounded straightforward at first. A washing machine had overflowed, spilling up to 100 gallons of water on a vinyl floor in a utility room, an entryway, hallway and part of a master bedroom. The contractor responded the same day, and took remedial actions immediately. Because there was a slight odor in the carpeted bedroom, the customer elected to remove the carpet and pad and schedule replacement with new. (Her son was very allergic to mold). The structure was then treated with a mildewcide/fungicide (spraying an antimicrobial is NOT what we recommend) and a dehumidifier and air movers were set up. The following day the contractor discovered that the wood floor assumed to be over a crawlspace, was in fact a
stringer type floor over concrete. The vinyl, obviously damaged and in need of replacement, was removed. Because the insulation between the stringers was contaminated due to a small chronic leak, the insulation was removed, the exposed stringers and floor was treated for mildew, and air was moved in the exposed areas. Within twenty-four hours the son was in the hospital in intensive care after experiencing an allergic reaction (apparently to mold). He had gone into respiratory arrest and almost died. Naturally, the contractor was concerned and started asking questions. After going back to the job, he found an area that was twenty feet away from the water damage he was working on where the stringers measured 30% moisture. This area had not been damaged in the current loss, yet it was wet. Upon questioning the customer, it was discovered that a year ago they had experienced water damage in the area where he was measuring the moisture. It sat for about six months and had been remodeled without structural drying. The second contractor had inadvertently moved this pre-existing mold with his drying procedures to dry the newly damaged area. He had removed 100% of all the affected material that he had seen and measured as having an elevated moisture content. He did not go into another room in an area that had not received any moisture from the current loss and measure... it just didn't seem called for. If the first contractor, during the remodeling, had addressed the problem of trapped moisture beneath the stringers and dried them, there would have been no problem with mold. Structural materials left to dry "on their own" usually take too long to dry, causing malodors due to biologic activity. Even the wrong equipment can take too long, such as drilling holes and letting a carpet dryer attempt to dry out the interior of a wall. Dry air has to be presented directly to the moisture laden material for drying to occur. When moisture is introduced into the area beneath the plywood, it will almost surely remain trapped unless dry air in sufficient quantity is introduced to enable the moisture to transfer to the air. The moist air is then moved out of the cavity and dehumidified.
I would caution that drying every false floor is neither practical nor advised. Some examples of problem situations or where you would not dry are:
|
Presence of pre-existing mold
|
|
Customer profile of allergies, asthma
|
|
Wet loose insulation
|
|
Delamination of plywood or other major structural problems such as wet or dry-rot
|
|
Vapor barrier with significant quantities of moisture trapped beneath it
|
|
Alternative demolition and replacement is less expensive
|
To dry a room you must have access to the areas along walls where the sleepers terminate (the butt ends). Carpeted areas should be disengaged from the walls and holes drilled between the 2" x 4" sleepers. A plastic barb can then be inserted into the hole. Pressurized air can then be injected into the plastic fitting through a drying system hooked up to a compressor providing enough air under pressure to overcome the resistance of the cavity. The other side of the room should be similarly disengaged and holes drilled to enable the air to escape from the cavity. Optimally, a drying system could operate on the other side of the room with negative pressure provided to both increase airflow and speed drying time. Switch the systems after several days to move air in the opposite direction to better equalize the substructure. Care must be taken to ensure that all areas are equalized and moisture contents of structural materials are below the danger point. Measurements must be taken in a manner that will enable you to measure moisture in the sleepers and in the insulation. This can usually be accomplished through the carpet, although it is much easier to measure with the carpet moved back.
Don't leave wet materials behind to cause health or structural problems for anyone, let alone you. If you dry thoroughly, you will not be the cause of a frantic phone call to 911.
by Ernie Storrer, President Inject-I-Dry Systems, Inc.